For years and years, companies have been following continuous improvement methodologies of one shape or size. Really, what we're doing is bringing that to the next level, by supercharging it with your plant's data and leveraging that data in order to gain insight about your equipment and processes. That all starts with the Digital Twin.
A Digital Twin is a representation of the physical environment around your asset. And, most importantly, what's happening with that asset at any given time.
Once we build out that Digital Twin, we then are able to use that to monitor what's going on around your assets, and provide reinforcing alerts and notifications when problems are identified. Then, learn from that data and history that we've been able to collect in order to gain insight and to solve key problems about your manufacturing process.
A Digital Twin, in the context of TwinThread, is the basis of performance transformation. A Digital Twin really is a collection of information about a piece of equipment in your plant. Things like different measures coming from SCADA systems, for example, allow you to drill in and see at any given point in time what's happening with the process. However, it's also information about key events that have occurred in the manufacturing process - things like when your equipment was up or down, or what product you're making. TwinThread's Digital Twins combined all that information together so that you can get a rich view of what happened with a piece of equipment. Once we have all this information together, this really empowers us to be able to analyze it in key ways, in order to understand the drivers of different issues that may be going on with your equipment, understand what the key measures are that influence your quality variation, or what process parameters are a key indicator of a particular problem about to occur.
Achieving this level of visibility is simple with TwinThread. We give you an easy way to configure and create those Digital Twins. We have a wizard that lets you map your data to the appropriate information for a given piece of equipment and quickly and easily configure a Digital Twin.
In each given use case that we work with, TwinThread provides you with a quick and easy way to configure a machine learning model, indicates what we're predicting, determines what information is being leveraged in that prediction, indicates how the data will be analyzed, and explains how the data will be filtered. We then output a whole slew of different analytical reports and views that allow your operations teams to understand, very deeply, what's going on about a given process and how your running efficiency can be transformed.
Our clients have achieved some amazing results by leveraging these techniques and have transformed their operations to drive improvements. All of this can be done in a very short period of time. Literally within weeks, you can go from connecting to those Digital Twins and building out that data model to uncovering some amazing analytical outcomes and insights to operationalize in your process.
If you'd like to learn more about how TwinThread can help your organization to solve industrial problems and get the most out of your equipment using Digital Twins as a foundation, please contact us or schedule a demo.
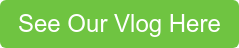

September 9, 2021