Colgate-Palmolive
Colgate implemented digital twins, won over its work force, saved money, and continues to make great product.
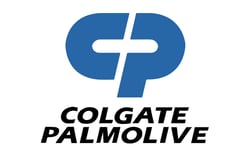
Colgate’s Six Best Practices in Deploying Digital Twins in Industrial Manufacturing
Colgate has been making products for over two hundred years – that’s right two hundred!
Some fun facts about Colgate:
- #1 market share in Toothpaste worldwide
- 59 consecutive years of dividend increases
- 5th consecutive year named to the Dow Jones Sustainibility Indices
Colgate’s sales are divided roughly evenly between emerging and developed markets, and 19% of their business is from their premium pet food division – Hill’s Pet Nutrition.
Colgate has embraced innovation as a corporate mainstay - with manufacturing, they are implementing new ways of working to instill a growth mindset to drive innovation with focus, empowerment, experimentation, and digitization.
Colgate has implemented TwinThread’s Industrial Operations Platform as a cornerstone of its manufacturing innovation strategy. They’ve achieved game-changing results with TwinThread’s digital twin and predictive operations technology. A digital twin is a representation of an asset or a process using the data known about it.
Game-changing technologies are only part of a successful project. A company has to operationalize, that is, put it into production, into daily direction setting, into the literal DNA of the plant, in order to achieve maximized results.
Below are six ‘must dos' from Colgate’s experience implementing TwinThread’s Industrial Operations Platform and its unique digital twin technology.
1. Use Smart Sensors Wherever Possible
“We decided to flow in as much of the data as we possibly could”
Sensor technology capabilities are increasing, and prices are declining every year. Use the digital twin project as an opportunity to invest in next generation sensing technologies capable of monitoring in-line product quality and other historically hard to measure variables to get even more information into your digital twin, and thus model and predict results more accurately.
"The black book and the human mind can only accept so much data, sensors can get closer to 100% data capture and are a good investment."
2. Data Quality
“Be a data hygienist”
Data quality is critical for training the model as well as real time streaming of information. Move away from manual and offline collection processes as soon as you can, thus solving the problem of inconsistent timing of samples or data checks, as well as the possibility of human error.
3. Embrace Automation as Quickly as Possible
“Eliminate the dull, dirty, dangerous tasks”
Wherever possible move away from manual methods of tracking operational data and responding to alert and alarm conditions. Use smart sensors or other technology to eliminate the possibility of human error and operator reluctance to deviate from their own standard practices. Colgate used TwinThread to both generate and respond to alerts, created a closed loop autonomous process free from human intervention, and reduced errors.
4. Ensure Visibility of Data
“People want to know the investment is paying off”
Provide the right KPI reports, visible to the right people – and make them role based. What’s important to an operator differs from a plant manager or a process engineer. Quantify improvements and celebrate successes. Colgate found this critical to employee acceptance and successful rollout.
5. Operationalize Early / Manage Change
"Don’t Wait"
A huge learning for Colgate was not to wait to operationalize – when a benefit it seen, and it’s better than existing practices, go for it, put it into production. And do it in a way that minimizes perceived changes to the operators. Colgate at first waited to operationalize and later regretted it – coming to understand that operator acceptance would best be achieved by early integration into their daily operating procedures.
An example was integrating TwinThread into current HMI screens and eliminating operator interaction where it wasn’t needed, through autonomous operations. Like Alexa, the HMI connects to many data sources but is a familiar interface to the operator. As a result, operators needed little training because it had been built into their regular work screens and processes.
"The operators are not only adapting to it, they’re living with it and seeing that it’s working."
6. Think Differently
"The most difficult part of this"
Create a culture that embraces new ways of working and doing so really involves all of the earlier learnings – lots of data, automation where appropriate, early operationalization, visibility of results. Colgate continues to use TwinThread to drive impactful operational results and is doing so even faster now by utilizing these best practices
Stay Connected with Industrial AI Trends and Platform Features
Get quarterly updates from our experts. Stay ahead with insights and strategies for digital transformation and operational excellence.