Global manufacturer of composite building materials implements Virtual Operations Center to improve asset performance and reduce energy intensity
Success Story
Highly asset intensive, energy intensive processes
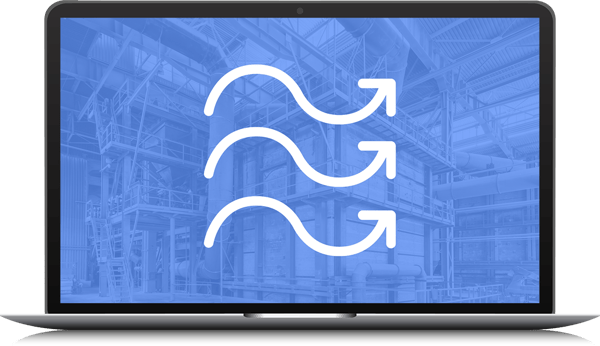
Success Story
Global manufacturer of composite building materials implements Virtual Operations Center to improve asset performance and reduce energy intensity
Access the extended PDF to read additional details.